RFID Warehouse Management: Things to Consider
Published on May 21, 2024
Written by: Mercom
In modern warehouse management, understanding the tools and technologies driving efficiency is crucial. RFID (Radio Frequency Identification) is frequently praised for its continual adaptation and refinement to suit modern needs. This tool reshapes how warehouses handle inventory, streamline operations, and maximize efficiency. In this article we’ll dive deeper into RFID warehouse management, exploring its applications, benefits, considerations, implementation strategies, and more.
Understanding RFID & Its Applications
What is RFID?
At its core, RFID is a technology that utilizes radio waves to automatically identify and track tags attached to objects. These tags store electronically encoded information that can be remotely retrieved and processed using RFID readers. Unlike traditional barcodes, RFID tags can be scanned at long range, up to 100 yards in some circumstances, enabling faster and more accurate data capture across various warehouse environments.
Why Do Warehouses Implement RFID?
Enhance Stock Management & GPS
RFID facilitates real-time tracking of inventory, providing precise location data throughout the warehouse. This enhanced visibility enables efficient stock management, reduces manual errors, and accelerates the retrieval of items, thereby optimizing warehouse operations.
Optimize Storage Data
By seamlessly integrating with Warehouse Management Systems (WMS), RFID enhances storage data accuracy and accessibility. This integration enables dynamic inventory management, improved picking accuracy, and streamlined replenishment processes, leading to enhanced operational efficiency.
Ensure Warehouse Safety
RFID technology plays a crucial role in ensuring warehouse safety by monitoring the movement of assets and personnel in restricted areas. By providing real-time tracking and visibility, RFID enables proactive risk mitigation measures, promotes adherence to safety protocols, and enhances overall workplace safety.
Considerations for RFID Implementation
While the benefits of RFID in warehouse management are substantial, several considerations must be addressed during the implementation phase:
Cost Considerations
The initial investment in RFID infrastructure, including tags, readers, and software integration, can be significant. However, the long-term benefits in terms of operational efficiency, inventory accuracy, and labor savings often justify the upfront costs. Moreover, advancements in RFID technology and economies of scale have led to cost reductions over time.
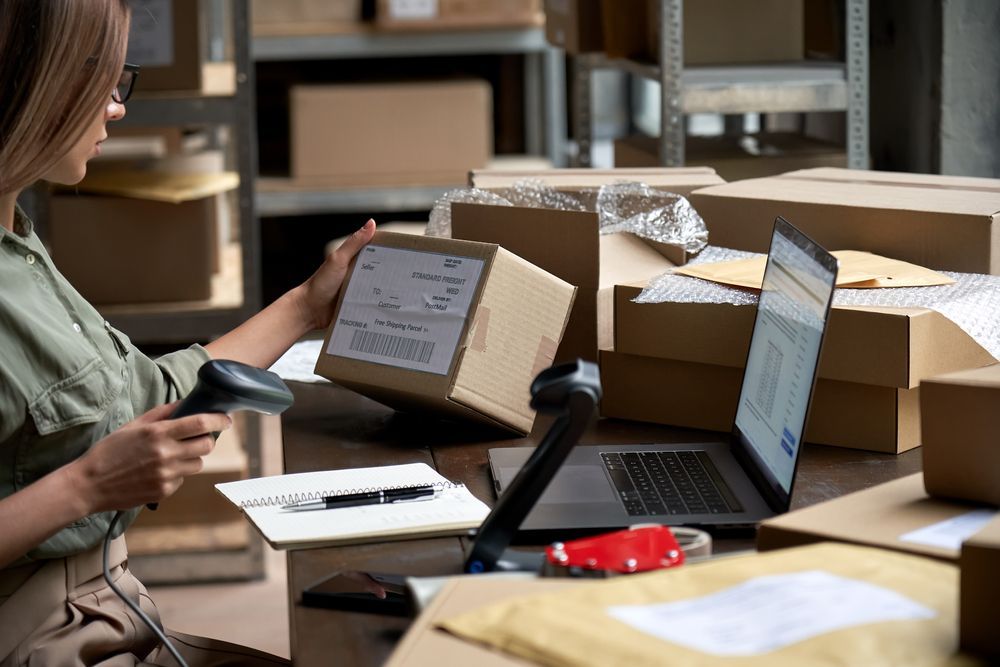
Standardization Challenges
Achieving compatibility and standardization across RFID systems, especially in multivendor environments, can be challenging. Addressing these issues requires careful planning, collaboration, and adherence to industry standards to ensure seamless integration and optimal performance. Connecting with seasoned RFID solution providers and industry groups can assist in effectively tackling these challenges.
Implementing RFID Technology in Warehouses
Implementing RFID technology in warehouses requires a strategic approach tailored to specific operational requirements:
Assessment & Planning
Conduct a comprehensive assessment of existing processes, infrastructure, and technology readiness. Develop a detailed implementation plan that outlines objectives, timelines, resource allocation, and performance metrics. Consider factors such as warehouse layout, inventory characteristics, and workflow dynamics to design an RFID solution that aligns with organizational goals.
Pilot Testing
Initiate small-scale pilot projects to validate RFID technology in real-world warehouse environments. Evaluate performance, identify potential issues, and refine the system before full-scale deployment to minimize risks and optimize outcomes. Engage stakeholders across departments to gather feedback and ensure buy-in throughout the implementation process.
Integration with Existing Systems
Seamless integration with existing Warehouse Management Systems (WMS), Enterprise Resource Planning (ERP) software, and other operational platforms is crucial for maximizing the benefits of RFID technology. Ensure compatibility, data integrity, and interoperability to facilitate smooth workflows and data exchange. Leverage Application Programming Interfaces (APIs) and middleware solutions to bridge communication gaps between disparate systems.
Common RFID Equipment
Handheld RFID Scanners: These portable devices are commonly used for inventory management, asset tracking, and retail applications. They allow users to capture RFID tag data quickly and efficiently while moving through a space.
Fixed RFID Readers: Fixed RFID readers are stationary devices typically mounted at entry/exit points, conveyor belts, or specific zones within a facility. They provide continuous monitoring and data capture of tagged items as they pass through designated areas.
Mobile RFID Readers: Mobile RFID readers are integrated into handheld devices such as smartphones or tablets. They offer flexibility and mobility, allowing users to scan RFID tags remotely and access real-time data from anywhere within a facility.
Wearable RFID Scanners: These scanners are worn by workers, usually in the form of wristbands or attached to clothing. They enable hands-free operation, making them ideal for applications such as order picking, inventory management, and logistics.
RFID Gate Readers:
RFID gate readers are installed at entry/exit points or specific locations within a facility to automatically capture tag data as items pass through. They are commonly used for inventory management, access control, and security purposes.
Desktop RFID Scanners: These compact devices are designed for desktop or countertop use, making them suitable for applications such as document tracking, library management, and retail point-of-sale (POS) systems.
These are just a few examples of common RFID scanners available on the market. The choice of scanner depends on factors such as the specific application, required features, scanning range, mobility requirements, and budget constraints.
Mercom is Here to Help!
Ready to optimize your RFID equipment for peak performance? At Mercom, we've got you covered with a comprehensive suite of services tailored to your needs. Whether it's hardware repair, asset management, refurbished equipment, or staging and deployment, our expert team is equipped to ensure your RFID technology operates seamlessly. Don't let equipment downtime or inefficiencies hold you back. Contact us today to discover how Mercom can elevate your RFID operations to new heights.